PV Industry Forum 2006 in Freiburg Part 2
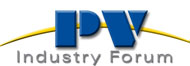
Despite the title, the afternoon session on reducing material consumption began with presentations by Schott Solar and Evergreen Solar on silicon ribbon techniques. The balance of the presentations concerned thin film technologies including a-Si (amorphous silicon), CIS (Copper-Indium-diSelenide), and CdTe (Cadmium Telluride). While seven technology/product presentations were made by the participating companies, only two companies have announced plans for 100MWp or greater production: Evergreen Solar and First Solar.
Silicon ribbon technologies grow a continuous silicon wafer from molten silicon using a vertical or horizontal pulling method, eliminating silicon “saw dust” or kerf losses of 30% or more through the wire sawing of silicon ingots/blocks. Evergreen Solar’s (ESLR) string ribbon technology, developed by Mobile Solar alumni, stole the spotlight with plans to expand the capacity of EverQ to 300MW by 2010. Renewable Energy Corporation ASA, (OSL:REC) has joined the EverQ joint venture between Evergreen Solar and Q-Cells (FRA:QCE), committing raw silicon supplies for the EverQ JV beginning in 2008.
First Solar burst on the worldwide solar industry in 2006 with aggressive capacity expansion plans for CdTe thin film solar modules on frameless, glass substrates. In the
GP View: Evergreen Solar continues to execute on their plans to commercialize and ramp their silicon string ribbon technology (Full disclosure: I own some shares of ESLR stock). First Solar appears to have an interesting CdTe thin film photovoltaic technology and an integrated product, production, and marketing strategy. The photovoltaic material properties of CdTe are superior to crystalline silicon, but First Solar will need to deliver modules at a lower cost per watt than crystalline silicon to succeed. In addition, First Solar must source their CdTe raw materials at competitive prices and evangelize their sustainable product life cycle vision to allay environmental fears about their heavy metal product content.
0 Comments:
Post a Comment
<< Home